読了目安:14分
鉄スクラップ考⑤ グリーンスチールとは?-現状と課題を考える
高炉大手メーカーのJFEスチールが、グリーンスチールを23年度上期から販売開始すると発表した。これにより、神戸製鋼所と日本製鉄を加えた高炉3社の製品が出揃った。本稿では、「鉄スクラップ考シリーズ」の第5弾としてグリーンスチールを取り上げる。
カーボンニュートラル実現の移行期に重要な鋼材
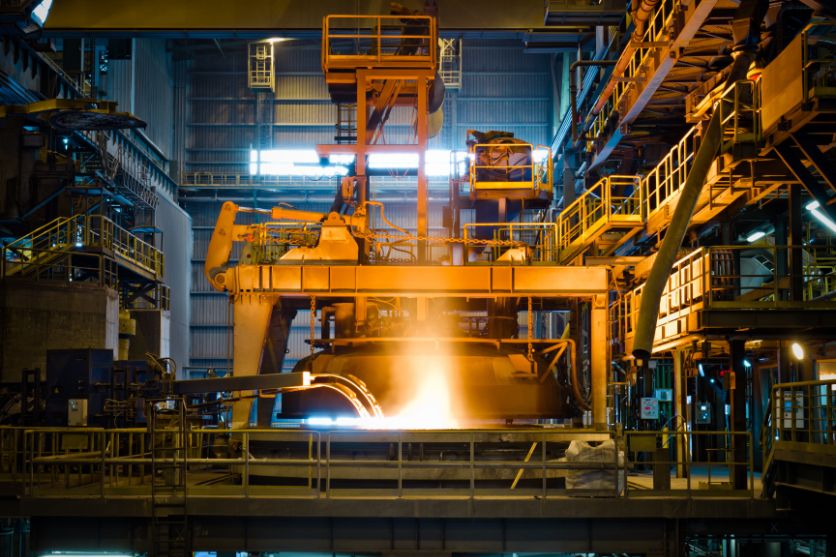
最近、グリーンスチールという言葉を良く耳にするようになった。そもそもグリーンスチールとは何なのか?
日本の鉄鋼メーカーの大手3社(日本製鉄、JFEスチール、神戸製鋼所)は、いずれも高炉メーカーである。
この高炉法による鋼材の製造は、還元反応の際に、石炭を蒸し焼きにしたコークスを投入する。このため、製造工程で多くのCO₂が排出されてしまうことが近年で大きな課題となっている(「鉄スクラップ考③ 鉄鋼産業のカーボンニュートラル実現への切り札」(2022年10月14日配信記事)参照)。
これに対し鉄鋼各社では、「2050年までに温室効果ガスの排出量をゼロにする『カーボンニュートラル』を目指す」ことを宣言している。
カーボンニュートラルを達成するための最終ゴールは「水素還元製鉄」(還元剤として石炭でなく水素を利用する)の実用化である。しかし、この製法はいまだ研究開発の途上であり、
- 技術的にクリアすべき多くの課題が残っていること
- 水素の安定供給体制の整備が必要なこと
が大きなハードルとなっている。
そこで、高炉各社がカーボンニュートラルの実現に向けた移行期間(トランジション期)として重要な役割と位置付けているのがグリーンスチールだ。
グリーンスチールとは、「自社技術を活用して、製造工程で温室効果ガスが発生しない、もしくは発生量を極力抑えて製造した鋼材」を指している。いわゆる低CO₂鋼材である。
マスバランス方式で「グリーン」の量を算定
では、グリーンスチールとは、どのようにして作られた鋼材のことを指すのだろうか?実は、グリーンスチールの算定には「マスバランス方式」という独自の算定方法が採用されている。
これは、製品の製造プロセスで発生する全体のCO₂排出量に対して、企業の努力で削減されたCO₂の量を一部の鉄鋼製品に集約させて、その鋼材を「グリーン」とみなす方式だ。
例えば、鋼材を100万トン製造している企業が自社の製造ラインの改善によりCO₂排出量の5%削減に成功したとしよう。この場合、数量全体の5%に相当する5万トンをグリーンスチールとみなすことになる(あくまでも「みなし量」であり、実際の製品である鋼材自体に違いがある訳ではない)。
なお、グリーンスチールの量の算定に当たっては、客観的な評価(外部の認証機関からの認証)を得なければならない仕組みとなっている。(参考までに、CO₂削減努力とは、具体的には、「低炭素化技術・プロセスの適用拡大」「省エネ・高効率化」「低炭素原燃料の活用」などを示している。)
先鞭をつけた神戸製鋼所
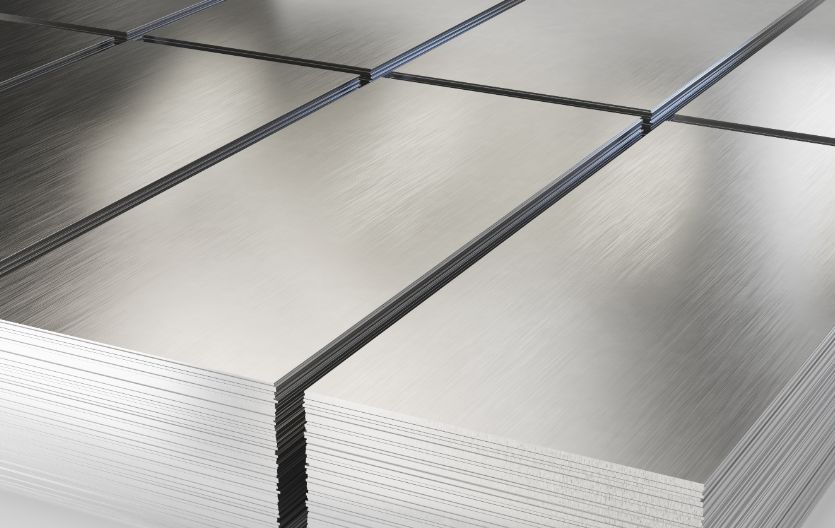
ここからは、高炉各社のグリーンスチールについてみていこう。
まず、最初にグリーンスチールを商品化したのが神戸製鋼所だ。22年5月に先陣を切って「Kobenable Steel」(コベナブルスチール)を発表した。
神戸製鋼所では、自社のエンジニアリング事業で展開するミドレックス(天然ガスを使った還元鉄製鉄法)技術を利用して製造したHBI(Hot Briquetted Iron)と呼ばれる半製品を高炉に投入することでグリーンスチールを製造している。
従来の高炉法では還元材としてコークスが使用されるが、これに代えて天然ガスを用いることから、CO₂排出量は、コークスを使用した場合と比較して20~40%削減できる。神戸製鋼所オリジナルの技術である。
コベナブルスチールの商品化が発表された翌月(22年6月)には、トヨタ自動車が競技車両「水素エンジンカローラ」のサスペンションメンバーへの採用を早々と表明、12月には日産自動車のミニバン「セレナ」への採用が発表された。
建設分野でも、12月に東京の豊洲地区再開発の新築工事に採用されたことが明らかになった。さらに今年2月には、今治造船のバルクキャリアへの納入も発表されている。
神戸製鋼所では、2030年には100万トン程度のグリーンスチールの供給を目指したいとコメントしている。
日本製鉄 供給量は年間30万トン
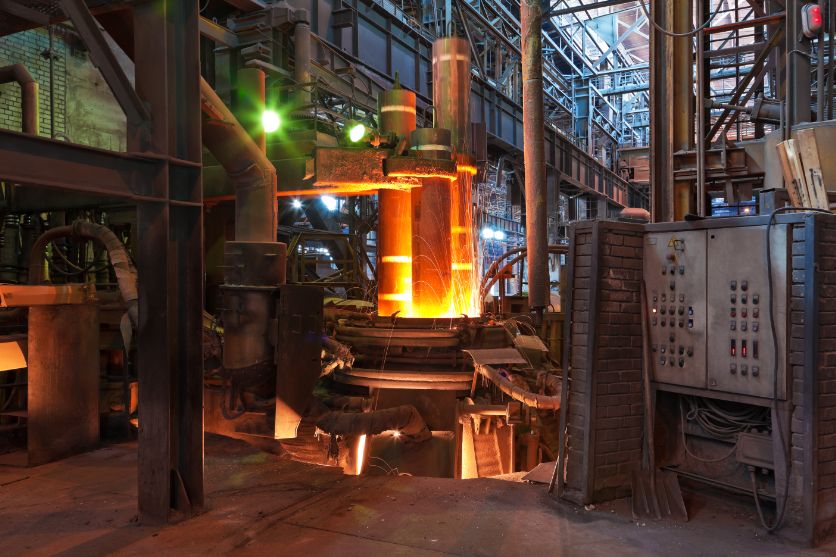
国内の高炉最大手である日本製鉄は、22年9月にグリーンスチール「NSCarbolex™ Neutral」(エヌエスカーボレックス ニュートラル)を発表、11月には高機能製品・ソリューション技術を総称するブランド「NSCarbolex™ Solution」を立ち上げた。
日本製鉄のグリーンスチールの核となるのが電炉の活用だ。過去の特集で述べてきたように、電炉法によって鋼材を製造した場合、高炉法を用いた生産と比較してCO₂発生量は4分の1程度に抑えられる。
日本製鉄では、カーボンニュートラルに向けての大きな柱の一つとして「大型電炉での高級鋼製造」を掲げている。まさにこれが、今回のグリーンスチールにつながっている。
日本製鉄では、エヌエスカーボレックスを発表した翌月(10月)には、瀬戸内製鉄所の広畑地区で研究中だった次世代電炉の商業運転を開始したと発表した。電炉化により削減されるCO₂相当の鋼材数量がグリーンスチールとして認証を受けている。
実際の出荷は23年9月から開始され、当面の供給量は年間30万トン程度となるもよう。
八幡地区の高炉 電炉に転換へ
さらに日本製鉄では今年5月10日、九州製鉄所八幡地区の高炉を2030年を目途に電炉への転換を目指すこと、並びに、瀬戸内製鉄所阪神地区と九州製鉄所八幡地区に900億円を投じて電磁鋼板の能力増強を実施することを発表した。
広畑地区で研究を重ねてきた電炉のノウハウを八幡地区へ活用していくことになるとみられる。
八幡地区といえば、1901年に官営八幡製鉄所として操業を開始した日本を代表する製鉄所だ。
橋本英二代表取締役社長は記者会見で、「脱炭素に対応できなければ、設立から120年の歴史を持つ製鉄所が、あと10年で幕を閉じることもありうる」とまで踏み込んだ発言をしており、電炉化の推進に対する強い決意が感じられる。
JFEスチール CO₂削減価値をサプライチェーン全体で生み出す初モデル
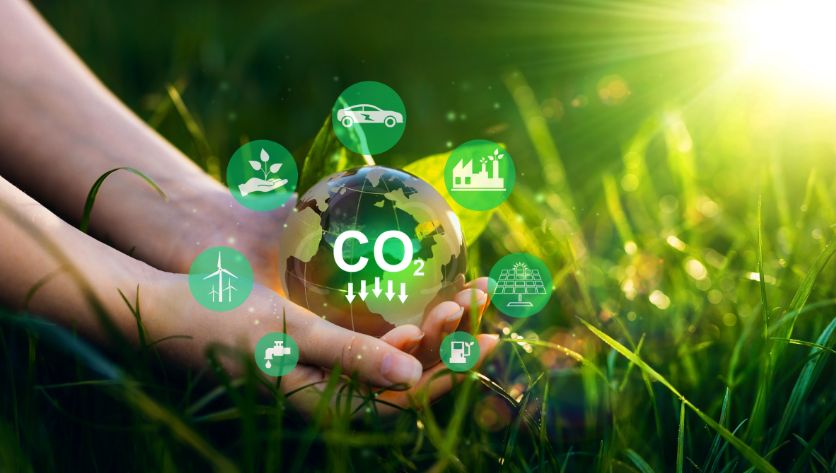
高炉3社の最後にグリーンスチールを発表したのがJFEスチール。今年5月8日に実施した22年度の決算発表に合わせ、グリーンスチールの概要を発表した。新ブランドの名称は「JGreeX™」(ジェイグリークス)。23年度上期中に発売を開始し、発売開始時点での供給可能数量は年間20万トン程度としている。
今回、認証機関から認証を得た削減量は、DRP®(Double-slag Refining Process)と呼ばれる独自の溶銑予備処理プロセスにより創出されたCO₂削減量である。溶銑予備処理プロセスとは、鉄鉱石を溶かす「溶鉱炉(高炉)」から出てきた半製品に含まれる不純物を除去するプロセスのこと。
JFEスチールでは、従来のプロセスに改良を加えることで、より大量の鉄スクラップを投入することを可能とした。これにより、原料の鉄鉱石から鉄スクラップへ代替が進むことになる。
ジェイグリークスの発表を受けて、早速6月20日には、国内海運8社が新規で建造を予定しているドライバルク船と、常石造船の水素燃料船への採用が決定した。
CO₂削減価値を鋼材価格に反映し、それをサプライチェーン全体で負担するモデルを初めて構築した。
拡大のカギ握るのは電炉
今回発表されたJFEスチールのグリーンスチールはDRP®プロセスをもとに算定されている。ただし、同社が今後、グリーンスチールを拡大させていく(将来的には数百万トンレベルを目指す)重要なアイテムとして位置付けているのは、日本製鉄と同様に電炉の活用だ。
JFEスチールでは、日本製鉄に先駆けて昨年9月、西日本製鉄所倉敷地区の高炉を電炉に置き換えることを発表している(「鉄スクラップ考④ JFEスチールが決断した高炉から電炉へのシフト」(2022年10月24日配信記事)参照)。
2027~30年の置き換えを目指しており、このタイミングで一気にグリーンスチールの生産量が増加することになる。今後の進捗に注目したい。
普及に向けた4つの課題
以上、みてきたように、高炉3社からの発表が出揃い、グリーンスチール市場が本格的に動き始めた。ただし、電炉などを活用したグリーンスチールの拡大に向けては、幾つかの課題が残されている。以下、順にみていこう。
課題1(制度面での課題)~規格の統一
グリーンスチールの最大の課題は、現状でまだ統一された規格が存在していないことだ。
現状では、各社が自社技術をもとに自らが選定した認証機関(国内外に様々な機関が存在している)から認証を受けているものの、明確な統一基準が定められていない。基準を明確にして標準化を進めていく必要がある。
課題2(制度面での課題)~ユーザーからのプレミアムの認識
高炉各社とも、独自の技術をもとにグリーンスチールを伸ばしていくために多額の研究開発費と設備投資を負担している(多大なコスト負担を強いられている)。
これをプレミアムとしてユーザーに受け入れられるかどうかも今後のグリーンスチール普及に向けての課題となる。マスバランス方式をもとに割り当てられた鋼材であるため、実際の鋼材製品自体は従来鋼材と違いはない。
それでも、鋼材ユーザーにとっては、自社製品が低CO₂鋼材を使用しているという付加価値(宣伝効果)は大きいはずである。
顧客がこの付加価値を認め、高炉各社のコスト増を適正なプレミアムとして販売価格に上乗せできるかどうかも、高炉各社にとってはグリーンスチール市場拡大に向けての大きなポイントと言えよう。
加えて言えば、政府による補助金の積み増しなども必要だ。
課題3(運用面での課題)~高級鉄スクラップの確保
電炉などを利用してグリーンスチールを製造するに当たっては、電炉に投入する鉄スクラップの確保が課題となる。
日本では粗鋼生産量の15年分に相当する大量の鉄鋼(建築物や自動車などとして実際に現状で使われている鉄の量)が蓄積されている(「鉄スクラップ考② 小資源国日本の貴重な資源」(2022年2月22日配信記事)参照)。
これらは将来の鉄スクラップ予備軍であり、一見すると原料が豊富に存在しているように見える。ところが、鉄スクラップにもグレードが存在する。
日本製鉄やJFEスチールが電炉での製造を目指している鋼材は、主に自動車用や造船用などに使用される高級鋼材である。このため、建築廃材などから取り出す不純物の多い低グレードの鉄スクラップは使えない。自動車工場で発生する打ち抜き屑など純度の高い高級グレードの鉄スクラップが必要とある。
高級スクラップの確保は、今後、大きな課題となってくるだろう。
課題4(運用面での課題)~グリーン電力の確保
日本の鉄鋼生産における電炉の製造比率は26%に過ぎず、米国(70%)、欧州(42%)などと大きな差がある。最大の理由は品質面での課題(不純物が多く含まれる電炉鋼材は高級鋼材の製造には適さない)だった。
ところが、近年の高炉メーカーによる技術革新により、品質面でのハードルはかなり低くなってきた感がある。一方、新たな課題として浮かび上がってきたのが電力だ。
電炉は「大量の電気で鉄スクラップを溶かして新しい鉄に再生する」ビジネスであり、溶解工程において短時間で大量の電力を消費する。
実は、国内の使用電力総量の2%を電炉が消費している。卑近な例でいうと、国内の標準的な規模の電炉を数10秒間稼働させただけで、一般家庭が一年間に使用する電力量を消費してしまう。
高炉各社は今後、設備を電炉に切り替えていくことを計画しているが、例えば国内鉄鋼生産における電炉比率を米国並みにまで引き上げるためには、現在の3倍近い電力を確保する必要があるのだ。
このため、
- 原子力発電所の再開が進まず引き続き石炭火力発電が主流である日本で安定した電力が確保出来るのか?
- 海外先進国と比較して割高な日本の電力料金で製造した鋼材で海外競合他社との競争力優位性が保てるのか?
などを解決していかなければならない。
再生可能エネルギーを利用したグリーン電力の確保などが必須となる。
オールジャパンで市場の拡大を
グリーンスチール市場はまだ始まったばかりであり、本格的に普及するまでには様々な課題が残されている。それでも、世界的なCO₂削減ニーズの高まりに応えていくためにも、伸ばしていかなくてはならない市場でもある。
高炉各社、鋼材ユーザー、政府、の三者が一体となってオールジャパンとして市場の拡大に向けて取り組んでいくことに期待したい。
▼関連記事はコチラ
鉄スクラップ考① 知られざる景気の先行指標
鉄スクラップ考② 小資源国日本の貴重な資源
鉄スクラップ考③ 鉄鋼産業のカーボンニュートラル実現への切り札
鉄スクラップ考④ JFEスチールが決断した高炉から電炉へのシフト
コメントが送信されました。