読了目安:14分
オペレーショナル・エクセレンスの基礎知識と事例3選~競合優位と業務効率化を目指す~
オペレーショナル・エクセレンスとは、現場で徹底的にオペレーション(業務の管理や実行過程)を改革することで、競合優位性の獲得を目指す考え方です。さらに、デジタルトランスフォーメーション(DX)が進む時代では、オペレーション改革の次の段階が求められます。そこで今回はオペレーショナル・エクセレンスの言葉の意味や特徴、事例を基に「実現する方法」を解説します。現場の業務プロセスに課題を感じている方は、ぜひ参考にしてください。
オペレーショナル・エクセレンスとは?組織能力で競合他社に差をつける
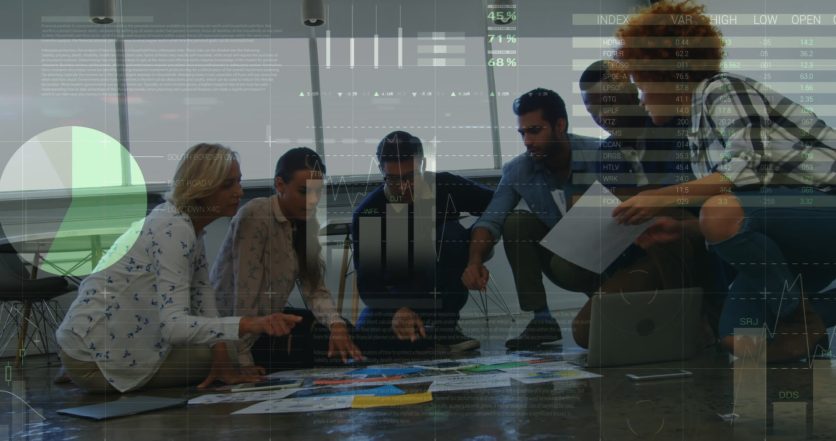
「オペレーショナル・エクセレンス(Operational Excellence)」とは、現場の業務遂行能力を磨き上げ、競合他社に差をつけることで優位性を獲得する考え方です。「オペレーション・エクセレンス」や「運用の優位性」と呼ばれたり、「OPEX」「OPE」「OE」と略して表現されたりすることもあります。
この概念は、アメリカの著名なコンサルタントであるM・トレーシーとF・ウィアセーマによって、1995年に著書『ナンバーワン企業の法則』の中で提唱されました。
革新的な製品やサービスを生み出す「プロダクト・イノベーション(Product Innovation)」や、顧客との親密な関係を築く「カスタマーインティマシー(Customer Intimacy)」と並び、優良企業の3大指標の1つとされています。
オペレーショナル・エクセレンスが注目された背景
オペレーショナルエクセレンスという概念は、1980年代にアメリカ合衆国が日本企業を研究する中で生まれ、日本に再輸入されました。
その後のグローバル化が進んだ現代では、企業競争が激しさを増しています。それに伴い、ビジネス環境の変化に対応するために、さまざまな企業がオペレーションの効率化に取り組んでいます。自社の強みを活かし、徹底的に組織構造を変革しなければ、他社との競争に打ち勝つことができないからです。
こうした状況のなかで、現場のオペレーションを改革し、競合他社からの優位性を得るための方法論として「オペレーショナル・エクセレンス」の実現が重要視されるようになりました。
オペレーショナル・エクセレンスの実現で得られる3つのメリット
オペレーショナル・エクセレンスの追求・実現には、次の3つのメリットがあります。
メリット1:改善のためのカルチャーが根付く
オペレーショナル・エクセレンスの追求により、業務フローだけでなく、業務フローを改善するプロセスそのものがマニュアル化され、常に良いオペレーションのために改善を重ねるカルチャーが現場の末端まで根付くとされています。
例えば、ファストフードチェーンのマクドナルドには、現場のちょっとした気づきを活かし、販売や接客のマニュアルを絶えず変化させるカルチャーが根付いています。
一度根付いた文化は簡単には失われません。競合他社から模倣されやすいプロダクト・イノベーションと違い、簡単には真似できない貴重な財産となります。
メリット2:部門を超えた全体最適化が図れる
生産、販売、企画・研究開発、サプライチェーンなどがシームレスに連携することで、組織の各部門が高いパフォーマンスを発揮する「全体最適化」を図れるとされています。
個々の現場だけでなく、企業を構成するあらゆる組織の効率化に取り組み、現場全体の高効率と高生産性を実現すると、製品・サービスの品質が上がり、顧客満足度やブランドイメージの向上にもつながるのです。
メリット3:組織の能力が底上げされる
オペレーショナル・エクセレンスでは、組織のケイパビリティ(総合的な能力)を最大限に生かすことが重要です。
前提として、組織によって得意なオペレーションは異なります。例えば、正確な仕事が得意な組織がある一方で、スピーディな作業に強い組織もあるでしょう。
こうした組織の特性を生かし「他社にはない組織能力」に昇華するのが、オペレーショナル・エクセレンスの特徴です。
また、人事異動や市場の動向などに左右されない標準的なオペレーションの実現によって、組織の属人化を防止できるという側面もあります。
オペレーショナルエクセレンスを実現する方法
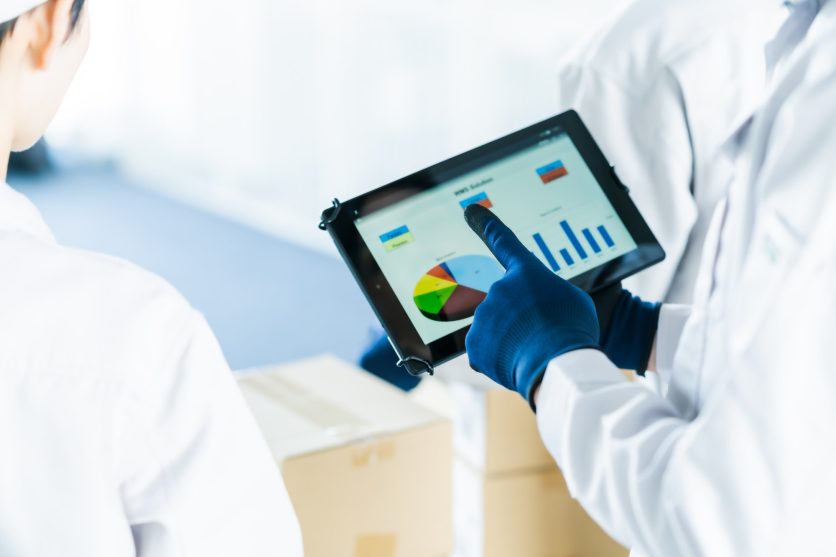
オペレーショナル・エクセレンスの実現には、現状の把握と改善の継続が必要です。各プロセスにおけるポイントを説明します。
現状の把握・課題の抽出
業務の現状と問題点を把握するにあたり、重要となるのは「業務の可視化」です。業務フローのマップ化や、ITツールの導入、現場で業務に携わる社員へのヒアリングなどを通して業務の分析を進めます。
可視化によって、組織全体で認識を共有できるだけでなく、業務工程において生産性の低下を招いているボトルネックの特定にもつながります。
継続的な改善
業務を可視化できたら、特定したボトルネック・課題に対して改善策を立てていきます。この際、「品質(Quality)」「コスト(Cost)」「納期・スピード(Delivery)」を軸に考えましょう。
メンバーのモチベーション低下を防ぐため、従業員エクスペリエンスを高めるという視点も重要です。
改善の計画は進行状況を都度確認し、必要に応じて修正を加える必要があります。ITツールの活用による進行管理の自動化も視野に入れると良いでしょう。
オペレーショナル・エクセレンスの代表モデル(方式)
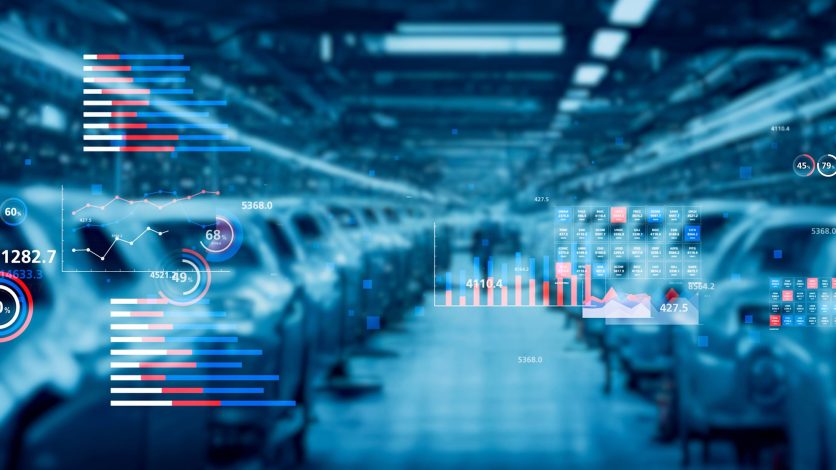
オペレーショナル・エクセレンスの代表的なモデル(方式)を具体的に見てみましょう。トヨタ自動車の「トヨタ式生産方式(リーン生産方式)」をはじめ、次の3つのモデルやフレームワークが定着しています。
【モデル1】現場の無駄をなくす「トヨタ式生産方式(リーン生産方式)」
トヨタ自動車の「トヨタ式生産方式」は、良い品質の製品を、無駄を徹底的に排除して生産する生産方式です。 ジェームズ・P・ウォマックがトヨタ生産方式を研究し、体系化した「リーン生産方式」と同様の内容になります。
トヨタ生産方式では「ニンベンのついた自働化」と「ジャスト・イン・タイム(JIT)」が重視されています。
「ニンベンのついた自働化」とは、機械ありきではなく、人間の知恵をもって「品質良く、安く、フレキシブルで、メンテナンスしやすい」生産ラインを築くことです。
一方ジャスト・イン・タイムは、「必要なものを、必要な時に、必要なだけつくる」という原則の下で無駄なく生産する考えです。リードタイムが長くなる完全受注生産と違い、各生産工程を連動させて、徹底的にオペレーションの無駄をなくすことに成功しています。
例えば、組立工程(後工程)で消費した部品を生産工程(前工程)に発注し、使った分だけ部品を納める「カンバン方式」が有名です。在庫と作りすぎの無駄をなくし、リードタイムを最小化する現場力を生かしたオペレーション改革といえるでしょう。
【モデル2】生産品質を追求する「シックスシグマ」
「シックスシグマ」とは、アメリカの電子・通信機器メーカーだったモトローラ社が開発し、生産現場の品質改善とコストダウンを達成したオペレーション改革です。
シックスシグマの「シグマ(σ)」とは、統計学における標準偏差(ばらつき)を意味しており、6σの範囲での生産品質のばらつきは、100万個のうち3〜4個です。
このことからシックスシグマは、不良品の発生を6σの範囲に抑えられるほどの精密な生産品質を目指した手法を意味しています。
【モデル3】トヨタ式とシックスシグマを合体させた「リーンシックスシグマ(LSS)」
「リーンシックスシグマ(LSS)」とは、アメリカのジェネラル・エレクトリック社(GE)が導入したことで有名なフレームワークです。
このフレームワークの特徴は、生産品質のばらつきをなくす従来のシックスシグマと、生産現場の連動により徹底してムダをなくすトヨタ生産方式を統合させた点にあります。
現場のリーダーによるマネジメントでは手が届きにくい部分も、現場力を活かして品質改善に取り組めるため、多くの一流企業が生産現場に取り入れています。
オペレーショナル・エクセレンスの改善事例3選
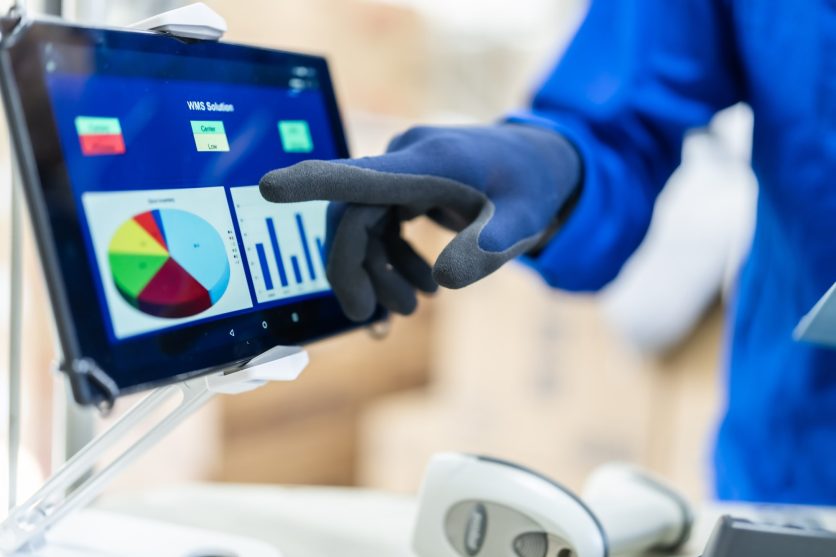
代表的なモデルとして紹介したトヨタ自動車のオペレーショナル・エクセレンスの他にも、様々なオペレーションの改善事例があります。
事例1:日本マクドナルドホールディングス株式会社
オペレーショナル・エクセレンスの実現事例として代表的なのは、マクドナルドの商品提供におけるプロセスの最適化です。
日本中に店舗があり、約19万人のクルーが働いていながら、店舗や従業員に左右されない商品のクオリティを保っているのには、製造や提供工程を詳細にまとめたマニュアルの存在が大きく関係しています。
2024年に日本マクドナルド株式会社の会長を退任したサラ・カサノバ氏が社長に就任してから、マニュアルに様々なケースが例示され、マンガや動画、ゲームなどでも学べるようになりました。
OJT※も取り入れられ、アルバイトやパートの入れ替わりが激しくても店舗が回るように、属人化の問題が解消されています。
※OJT(On the Job Training)…職場で実務を通して行う従業員の教育のこと。
事例2:味の素株式会社
味の素では、オペレーショナル・エクセレンスを全グループで標準実装しています。
主な取り組みは次の3つです。
- 顧客と顧客の求める価値の定義
- 目標設定と分解
- データに基づくマネジメント
顧客と顧客が求める価値を定義し、組織と個人の目標、KPIを設定し、施策に取り入れるというプロセスでオペレーションの改革を実施しました。
組織と個人の目標を設定するにあたって行った徹底的なディスカッションが、味の素のオペレーショナル・エクセレンスにおける特徴です。個人の目標と成果、成長のための提案をプレゼンテーションする手法がとられています。
活発なディスカッションによってそれぞれが持つデータに焦点があたり、データマネジメントプラットフォームを用いたデータの統合が進むなど、DXの推進に繋がりました。
▼参考記事はこちら
味の素グループの全社オペレーション変革の取り組み
事例3:株式会社リコー
リコーは、デジタル技術とデータを活用して業務プロセスを変革する「プロセスDX」に取り組み、オペレーショナル・エクセレンスの実現を目指しています。
プロセスDXは業務・作業の可視化に始まり、プロセスの最適化、デジタルツールの活用、データを利活用したモニタリングの実施という流れで進行し、改革に必要なスキルを習得させる人材育成にも注力しています。
結果、ストレスからの解放や価値の高い業務への従事などといった定性的な効果に加え、自動化による年間約550,000時間の工数削減といった効果につながりました。
DX時代のオペレーション改革とは?自動化・自律化に向けたオペレーションの再定義
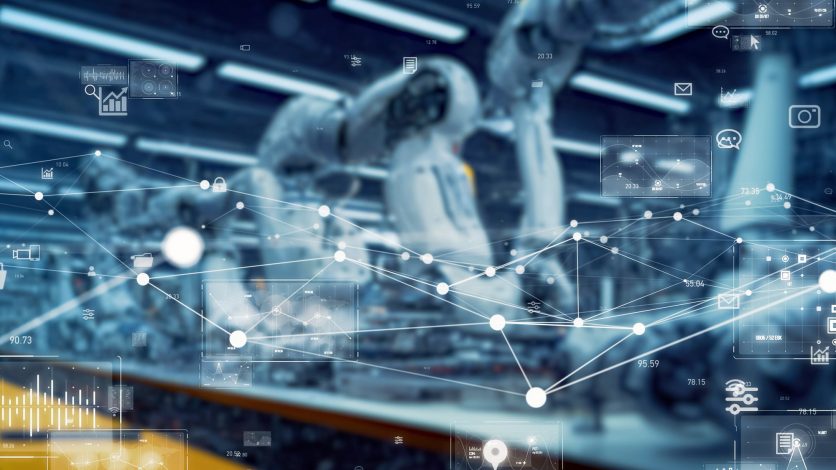
前述の通り、オペレーショナル・エクセレンスの実現には、オペレーションの改革が必要です。最後に、DX時代におけるオペレーション改革について考えます。
「デジタルトランスフォーメーション(DX)」とは、スウェーデンのエリック・ストルターマン教授が提唱した概念で、「デジタル技術を世の中に浸透させ、人々の生活をより豊かなものに変化させる」ことを意味します。
IoT、AI、RPA、ロボティクス、ブロックチェーンなどのテクノロジーが実用段階に入ったDX時代では、従来とは異なるオペレーション改革が必要です。
「定型化・単純化」から「自動化・自律化」の時代へ
以前のオペレーション改革では、生産現場の前工程と後工程が緊密に連携するカンバン方式や、現場の優れた管理者がリーダーシップを発揮するシックスシグマなど、人手によるオペレーションの単純化・定型化が中心でした。
しかし、IoTやAIなどの導入が製造業で急速に進み、人手のかからない自律的なオペレーションが増えつつあります。
そのため、人的リソースを機械化する従来の手法だけでなく、デジタルテクノロジーに対応したオペレーション改革を行わなければ、DX時代で競合優位性を保つことは難しいでしょう。
人員の再配置や新たなフレームワークも必要に
生産現場の自律化によって現場の余剰人員が発生すれば、その人員を再配置し、新たな価値を創出してもらうためのフレームワークも求められます。
従来のオペレーショナル・エクセレンスに頼り切るのではなく、自社の企業価値を再定義し、現場全体でイノベーションを起こすことが重要です。
DX化など組織の現状に適した業務改革を
いかがでしたでしょうか?今回は、業務効率の向上に寄与するオペレーショナル・エクセレンスについて解説しました。
オペレーショナル・エクセレンスによる改善が重要な一方で、オペレーション以外にも改善すべき点は多く存在します。
その改善点はビジネスモデルや人材の管理にあるかもしれません。企業を成長させるためには、様々な要因を複合的な視点で分析する必要があるでしょう。
▼関連記事はこちら
BPR(業務改革)とは何か? BPMやCMMIとの違いとともに業務効率手法を探る
カスタマーインティマシーとは?顧客と親密になって価値を生む戦略を解説
ネットスーパーで提携加速 楽天&西友など 激動の一年を振り返る
コメントが送信されました。